Nitrogen generator solution to replace liquid nitrogen for laser cutting
Why Nitrogen Generators are Essential for Laser Cutting
Nitrogen plays a critical role in enhancing the safety of laser cutting processes. During cutting, maintaining an inert atmosphere by using nitrogen helps prevent the risk of combustion and oxidation, which can lead to fire hazards. By displacing oxygen, nitrogen limits the potential for these reactions, ensuring a safer working environment for operators.
Furthermore, the use of nitrogen during laser cutting significantly improves cut quality. It aids in achieving lower dross formation and prevents material warping by facilitating effective heat dissipation. This results in smoother edges and a more aesthetically pleasing finish, ultimately enhancing production efficiency. The improved cut quality means fewer touch-ups and refinishing, translating into faster turnaround times and increased output. Hence, nitrogen generators are indispensable for ensuring consistent, high-quality results in laser cutting operations.
Advantages of Nitrogen Generators Over Liquid Nitrogen
Cost Efficiency of Nitrogen Generators
Nitrogen generators offer significant cost savings over liquid nitrogen. By eliminating the need for regular delivery and storage, businesses can achieve greater economic efficiency. The costs associated with third-party suppliers and frequent downtimes due to waiting for nitrogen supplies are all but removed. This self-sufficient system allows for the production of nitrogen on-site, presenting an economical solution for enterprises looking to optimize their operational budgets.
Environmental and Operational Benefits
Incorporating nitrogen generators also results in substantial environmental and operational advantages. By reducing the need to transport liquid nitrogen, businesses can significantly lower their carbon footprint, aligning with sustainability goals. Moreover, generators provide a continuous supply of nitrogen, which enhances operational flexibility and minimizes the disruption often suffered due to supply chain limitations. This reliability ensures that production processes continue smoothly without unexpected halts due to nitrogen shortages.
High-purity 99.99% Nitrogen Generator for Laser Welding
Features and Benefits
The High-purity 99.99% Nitrogen Generator is designed to ensure optimal performance in laser welding applications by significantly minimizing impurities that could compromise weld quality. This level of purity is crucial for achieving consistent, high-quality results. Enhanced features such as real-time monitoring and automatic adjustments further cater to changing operational needs. These technological advancements streamline workflow and reduce the need for operator oversight, allowing businesses to focus on precision and efficiency.
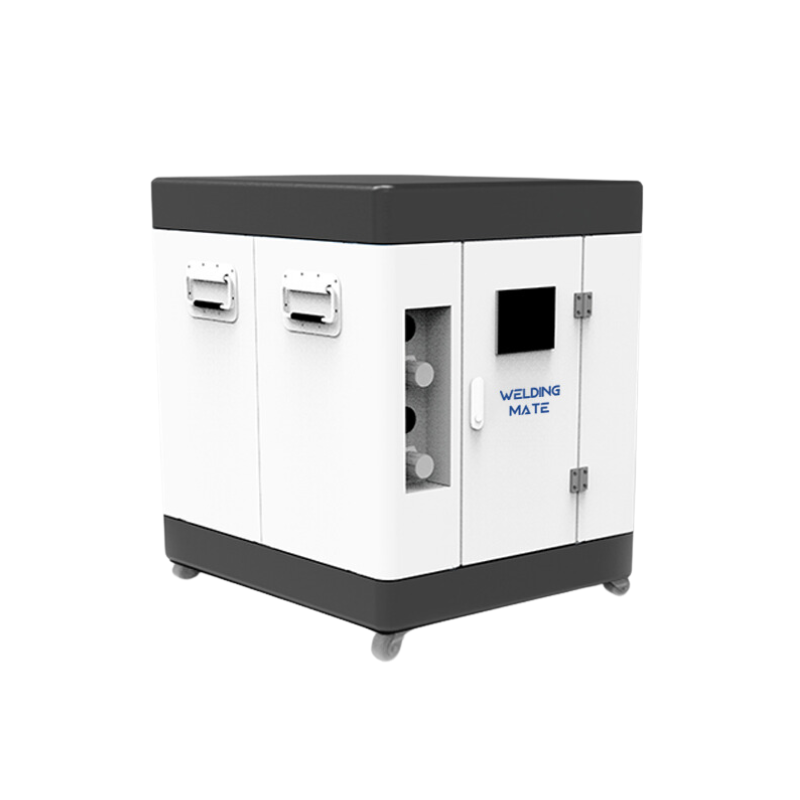
Integration and Operational Efficiency
This nitrogen generator seamlessly integrates with existing laser systems, allowing users to quickly adapt to new workflows without disrupting ongoing operations or requiring extensive retraining. By providing a reliable and stable nitrogen source, operational efficiency is significantly enhanced. This stability supports increased production rates by eliminating the uncertainties associated with external nitrogen supply, ensuring that production can continue smoothly without interruptions.
Incorporating this nitrogen generator into your laser welding operations not only improves process control and output quality but also aligns with modern industrial demands for precision and efficiency in production.
Choosing the Right Nitrogen Generator for Your Needs
Key Factors to Consider
When selecting a nitrogen generator, factors such as required flow rates and purity levels are crucial. In laser cutting or welding applications, it's vital to ensure the chosen generator meets specific operational needs by providing optimal gas output. Assessing these factors depends on the application requirements—such as material type and process intricacies—which help in identifying generators that align with the necessary standards. Additionally, evaluating space and installation considerations is important, ensuring the generator not only fits within facility constraints but also maintains accessibility for maintenance and operation.
Customization Options
Many manufacturers offer customization options to address diverse business needs effectively. For instance, organizations can select tailored output levels and features that best align with their process requirements, ensuring that their nitrogen generator is as efficient and cost-effective as possible. Furthermore, considering future scalability when choosing a generator can facilitate growth, allowing system upgrades without necessitating complete replacement. This forward-thinking approach ensures that the device remains a viable part of the infrastructure as business scales.
Implementing Nitrogen Generators in Your Laser Cutting Process
Installation and Setup
Proper installation and setup of nitrogen generators in laser cutting processes are crucial for ensuring consistent production quality and efficiency. To achieve this, the generators must be meticulously calibrated to produce nitrogen at specified purity levels essential for high-precision cutting. By planning the layout effectively, you'll enhance safety and workflow within the facility. An optimal layout ensures the generator is positioned for efficient airflow, minimizing potential disruptions and reducing the risk of downtime.
Maintenance and Long-term Use
Maintaining nitrogen generators in laser cutting operations involves regular checks and timely filter replacements to prolong their life and ensure consistent performance. Scheduled maintenance plays a critical role in preventing costly repairs, as it helps identify and mitigate issues before they escalate. Furthermore, training personnel in monitoring and upkeep best practices enhances system reliability. By doing so, businesses can maintain maximum uptime, ensuring that laser cutting processes proceed without interruption, ultimately leading to increased operational efficiency.
FAQ
What role does nitrogen play in laser cutting?
Nitrogen creates an inert environment that prevents oxidation and combustion during laser cutting, improving safety and cut quality.
How do nitrogen generators compare with liquid nitrogen in terms of cost?
Nitrogen generators are more cost-effective as they eliminate expenses related to delivery and storage while providing a continuous on-site supply.
What should be considered when choosing a nitrogen generator?
Consider flow rates, purity levels, application needs, space requirements, and future scalability when selecting a nitrogen generator.