The difference between membrane nitrogen generation and PSA (Pressure Swing Adsorption) nitrogen generation
Understanding Membrane Nitrogen Generation
Membrane nitrogen generation is a powerful method that separates nitrogen from other gases through selective permeation. This process does not rely on chemical reactions, making it both efficient and cost-effective. By allowing only nitrogen molecules to pass through its special membranes, this technology ensures a consistent supply of this vital gas without the need for complex or hazardous procedures.
The gas separation mechanism in membrane technology hinges on the diffusion rates of different gases. Due to their varying speeds through the membrane, gases such as oxygen and carbon dioxide, which diffuse faster, are separated from nitrogen, which moves more slowly. This selective permeability makes membrane generators suitable for applications where lower purity levels of nitrogen are sufficient, thus optimizing resource allocation.
Membrane systems generally comprise hollow fiber membranes, feed gas compressors, and nitrogen storage tanks. These fibers are engineered to selectively allow nitrogen molecules to pass while excluding others, enhancing the purity and efficiency of production. By optimizing the materials and design, these systems achieve efficient nitrogen separation, reducing the need for frequent maintenance and ensuring continuous operation.
The design and material of the membranes are crucial for their performance and durability. Advanced materials in membrane production can significantly boost their operational lifespan and efficiency, thereby optimizing performance over time. Therefore, technological advancements in membrane materials are continuously enhancing the capabilities and applications of membrane nitrogen generators in various industrial settings.
Exploring PSA Nitrogen Generation
Pressure Swing Adsorption (PSA) is an efficient technology utilized for nitrogen generation. It operates by adsorbing nitrogen from compressed air, thereby separating nitrogen molecules from oxygen and other contaminants. This process hinges on the selective adsorption properties of materials such as zeolite or activated carbon, which play a crucial role in retaining oxygen and other gases under high pressure, while allowing nitrogen to pass into storage tanks. This selective adsorption ensures high-purity nitrogen essential for various industrial applications.
Understanding the cycle of pressurization and depressurization within PSA technology is key to appreciating its effectiveness in producing high-purity nitrogen. During the pressurization phase, compressed air passes through vessels filled with adsorbent material, causing the separation of gases based on their molecular characteristics. The nitrogen flows out into a storage system, while the oxygen remains absorbed. The subsequent depressurization phase allows oxygen and other absorbed gases to be expelled, regenerating the adsorbent material for the next cycle. This cyclic process highlights the advanced engineering behind PSA technology.
The scalability of PSA systems makes them highly adaptable for diverse industrial applications, ranging from small-scale to large-scale nitrogen production facilities. Their capacity to produce nitrogen with varying levels of purity, often exceeding 99.999%, positions them as a preferred choice in industries like electronics and pharmaceuticals that require stringent purity standards. Additionally, the availability of PSA nitrogen generation technology across different capacities ensures flexibility, making it possible to meet specific needs and operational scopes efficiently.
Comparing Membrane and PSA Nitrogen Generators
When it comes to nitrogen purity levels, PSA nitrogen generators surpass membrane systems significantly. PSA nitrogen generators are capable of achieving purity levels as high as 99.999%, which is ideal for applications requiring extremely high purity. In comparison, membrane nitrogen generators generally produce nitrogen with purity levels ranging from 95% to 99%. This makes membrane systems more suitable for less critical applications where such high purity is not required.
In terms of operational efficiency, the two systems cater to different niche requirements. Membrane nitrogen generators are more energy-efficient when producing lower purity nitrogen, making them cost-effective for applications that do not demand the highest purity levels. Conversely, PSA systems excel in scenarios that demand high-purity nitrogen despite possibly higher operational costs. The comprehensive nature of PSA technology, with its pressurization and depressurization cycles, contributes to this efficiency for high-purity needs.
Maintenance requirements also differ between the two technologies. Membrane systems benefit from having fewer moving parts, resulting in less complex maintenance; usually, this involves replacing membranes periodically. On the other hand, PSA systems necessitate regular monitoring and replacement of adsorbents to ensure their optimal operation, which could be more labor-intensive but essential for sustaining their higher output purity.
Applications of Membrane and PSA Nitrogen Generators
Membrane nitrogen generators are prominently utilized across various industrial domains, owing to their efficiency and cost-effectiveness. Industries such as packaging, oil and gas, food preservation, and laser cutting benefit from these generators. They provide a practical solution for environments requiring mid-range purity levels, generally ranging from 95% to 99%. Their low operational costs and ease of installation make them a favorable choice for businesses looking to streamline nitrogen supply without compromising on efficiency.
On the other hand, PSA nitrogen generators are extensively adopted in sectors demanding high-purity nitrogen, such as the medical and pharmaceutical industries. These systems are crucial for operations like inerting, blanketing, and preserving sensitive materials, where maintaining a purity level of up to 99.999% is essential. This ensures the protection and longevity of products sensitive to oxygen and moisture exposure, thereby enhancing the quality and safety of healthcare and pharmaceutical processes.
Both membrane and PSA nitrogen generators can be customized to meet specific industrial demands, offering a flexible approach to nitrogen generation. By tailoring these technologies to suit particular applications, industries can achieve the desired purity and flow rates, ensuring operational needs are precisely met. This adaptability highlights the crucial role of nitrogen generators in enhancing industrial efficiency and safeguarding product integrity across various sectors of the economy.
High-purity 99.99% Nitrogen Generator for Laser Welding
This high-purity nitrogen generator is specifically designed for laser welding applications, which demand an inert environment to prevent oxidation and ensure superior weld quality. The generator produces nitrogen at 99.99% purity, essential for protecting welding joints and equipment. Utilizing this generator over traditional bottled nitrogen significantly reduces operational costs, ultimately enhancing efficiency in manufacturing processes.
The advantages of this generator include not just high nitrogen purity, but also a dramatic reduction in operational costs compared to using bottled nitrogen. The system supports seamless integration with portable laser welding machines thanks to its compact size and lightweight design. This feature allows for both built-in and externally mounted configurations, making it versatile for various welding setups. Additionally, the intelligent start-stop and automatic venting functions ensure consistent output and efficient operation, resulting in minimal downtime and maintenance demands. This capability makes it economically viable and operationally reliable.
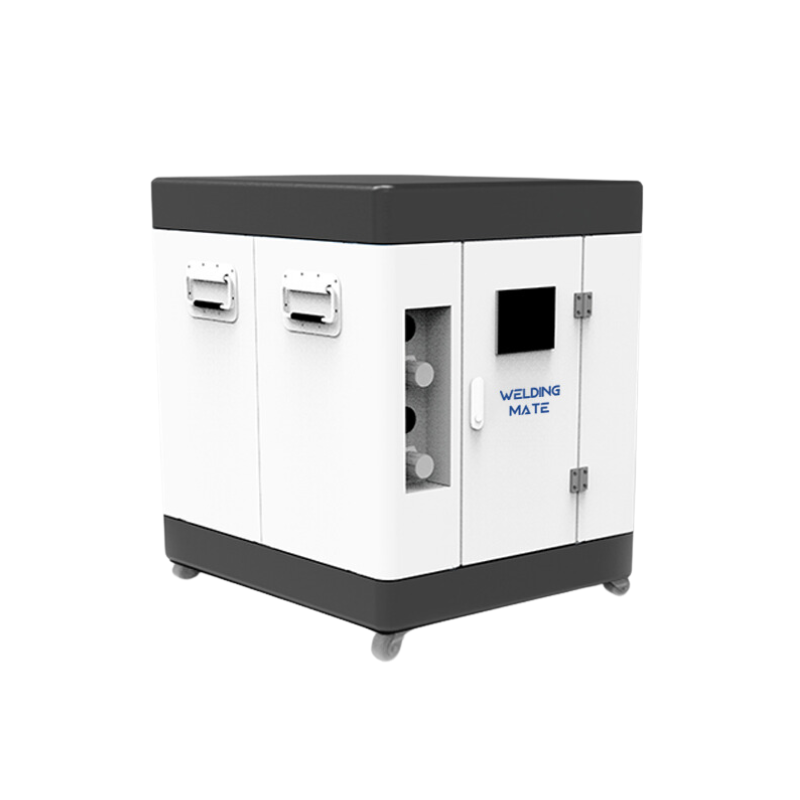
FAQ
What is membrane nitrogen generation?
Membrane nitrogen generation is a method that separates nitrogen from other gases through selective permeation without chemical reactions. It uses special membranes to allow only nitrogen molecules to pass through, providing a consistent supply of nitrogen efficiently and cost-effectively.
How does a PSA nitrogen generator differ from a membrane nitrogen generator?
PSA nitrogen generators offer higher purity levels (up to 99.999%) compared to membrane systems (95% - 99%). PSA is suitable for applications demanding high purity, while membrane systems are efficient for mid-range purity levels with lower operational costs.
For which industries are PSA nitrogen generators suited?
PSA nitrogen generators are ideal for industries requiring high-purity nitrogen, such as electronics, pharmaceuticals, and healthcare. They are used in processes like inerting, blanketing, and preserving sensitive materials.
What are the benefits of using a nitrogen generator for laser welding?
A nitrogen generator for laser welding provides high-purity nitrogen (99.99%), reduces oxidation, ensures superior weld quality, and lowers operational costs compared to traditional bottled nitrogen.